Fan support bearings require particular attention when devising a lubrication strategy. Because a broad range of bearing types can be employed it is important to understand the bearing and seal types before proceeding. This information is critical in order to understand the optimal grease delivery points, grease flow paths, the requirements for efficient grease exchange and the point(s) of grease exit from bearing housings.
During the implementation of perma STAR VARIO it is important to address the following items:
- Ensure that the bearing housing is correctly packed with grease in order to ensure efficient grease exchange. This is especially important for bearing types which must be re-lubricated from the side, rather than via a central re-lubrication groove.
- Where contact seals which are not free purging are in use, such as double lip seals, ensure that a suitable point for grease relief is introduced to the housing in order to avoid over-lubrication.
- Consider the use of high performance greases which can withstand the high rate of mechanical work which is applied by high speed rolling element bearings such as spherical roller bearings.
Challenges
Blowers and fans are often used in extreme operating conditions with many contaminants in the air. Dust and other substances entering the bearing system will lead to increased wear of individual components and a shorter service life of the fan.
Regular lubrication of bearings and seals is essential for uninterrupted operation. Fan and blower lubrication points are often extremely dirty and hard to reach, which makes maintenance even more difficult. When manufacturer recommended lubrication intervals are not observed, the system will eventually fail as a result of lubricant starvation.
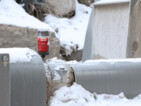
Contaminants (e.g. dust) raised in the air must not enter the lubrication points
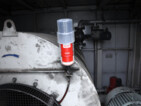
Excessive overheating of bearing points due to lubrication starvation
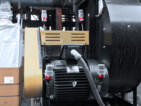
Lubricants must be able to withstand demands, such as vibrations and high speeds
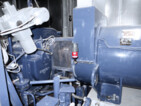
Observing relubrication intervals (depending on bearing type, bearing size and ambient conditions)
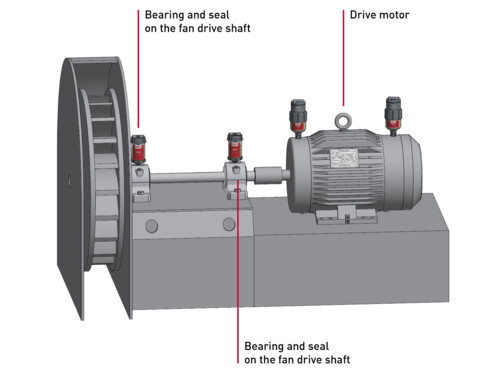
Lubrication points
The lubrication points (roller bearings) are located at the drive shaft between drive motor and fan impeller.
Bearing and sealing of fan drive shaft is normally done by means of a pillow block housing or a bearing unit. These must be permanently supplied with the specified amount of the right lubricant.
Solutions
Mount a perma lubrication system at the lubrication point. Depending on the conditions prevailing at the lubrication point, the perma lubrication system can either be mounted directly or remotely.
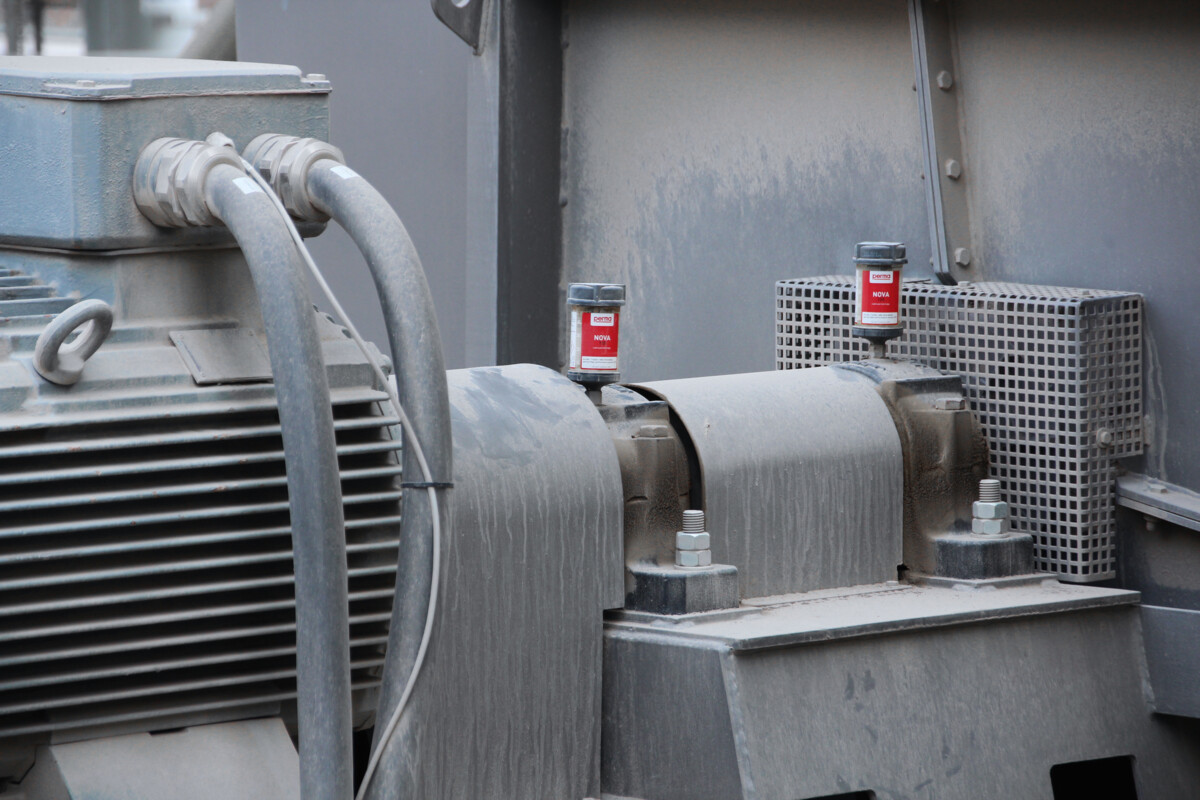
- Easy, quick mounting
- For lubrication points with little vibration / shocks
- For easy-to-reach, safe lubrication points
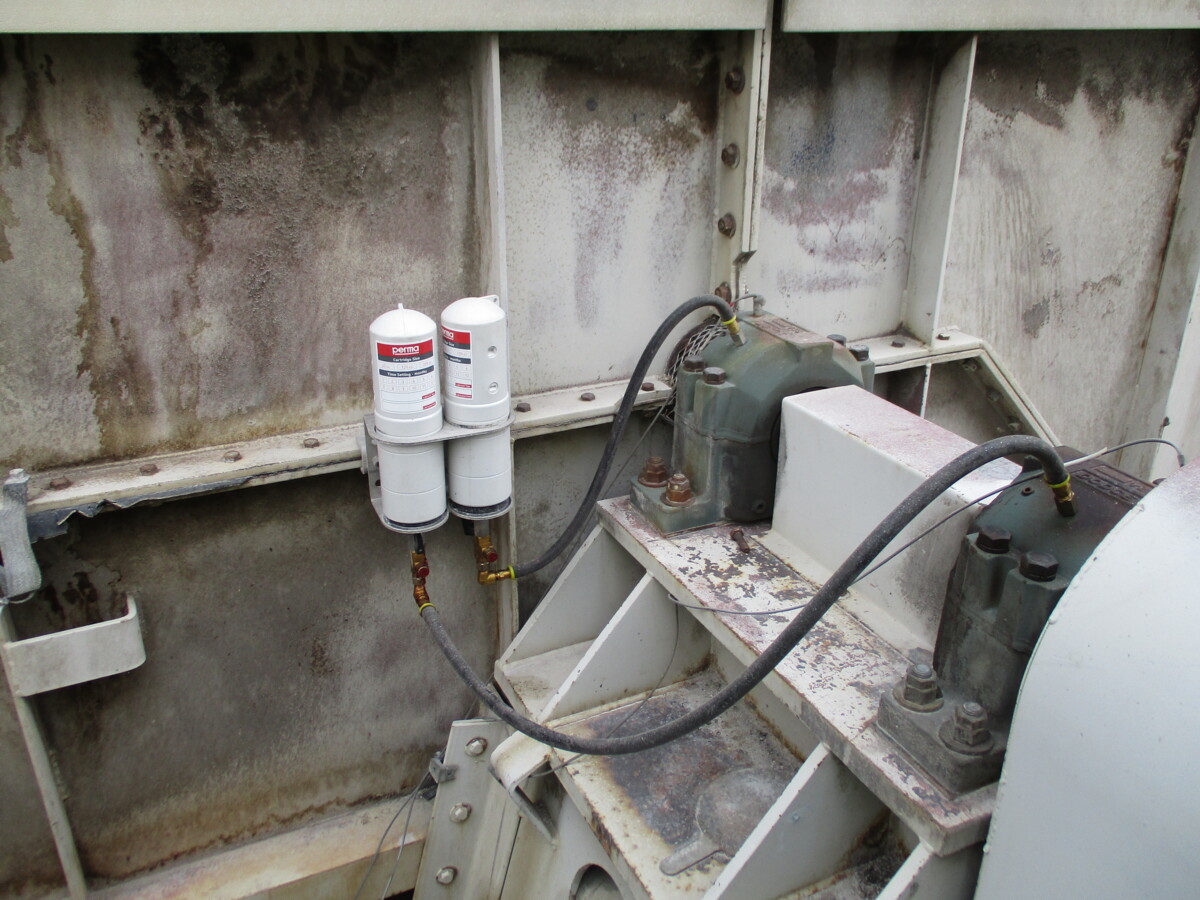
- For lubrication points with strong vibration / shocks (isolation of lubrication system)
- For lubrication points which are unsafe to access: Mounting in safe areas
- For hard-to-reach lubrication points
Any more questions?
Simply contact us by phone or email for an individual consultation on blowers / fans.
Advantages of automatic lubrication
No contamination
perma lubrication systems seal lubrication points and protect against contamination
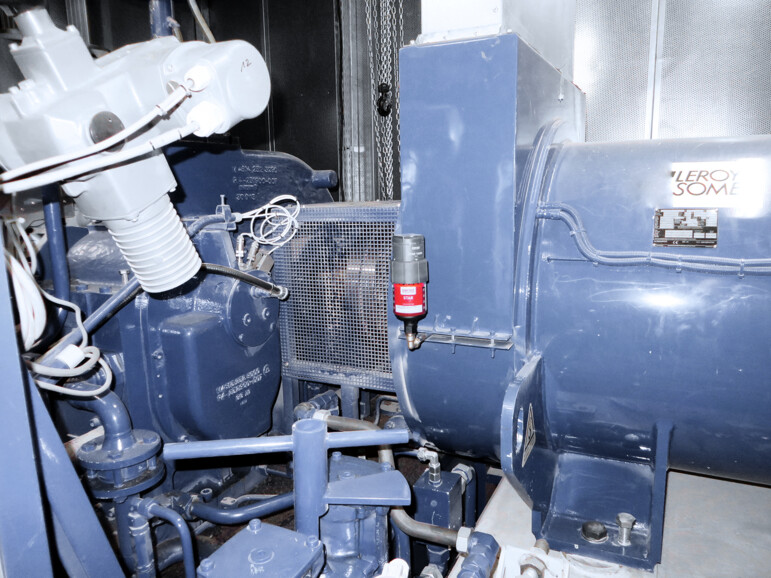
Precise metering
Precise metering of lubricant amount reduces lubricant consumption
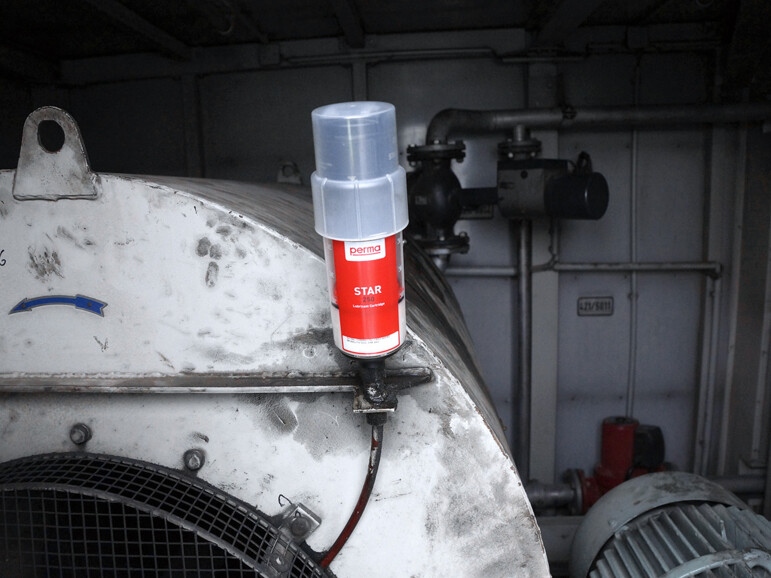
Safe lubrication
Safe and reliable lubrication, also in areas with potentially explosive atmospheres
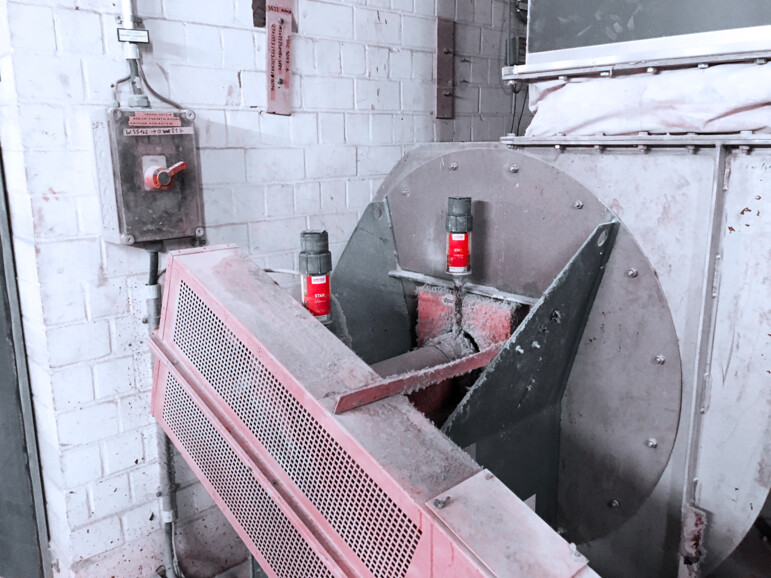
Exact adjustment
Different lubricant volumes for precise discharge settings to meet lube-point requirements
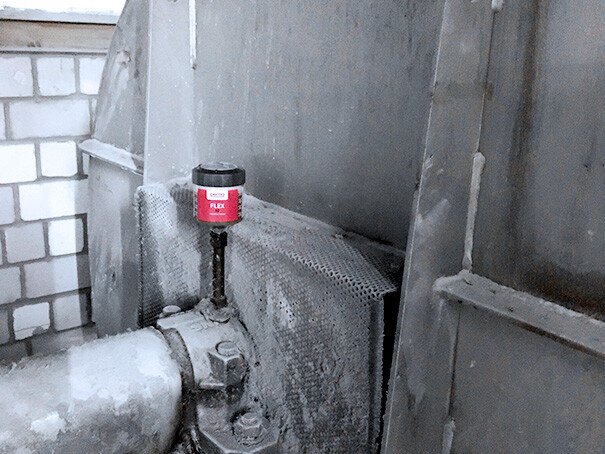
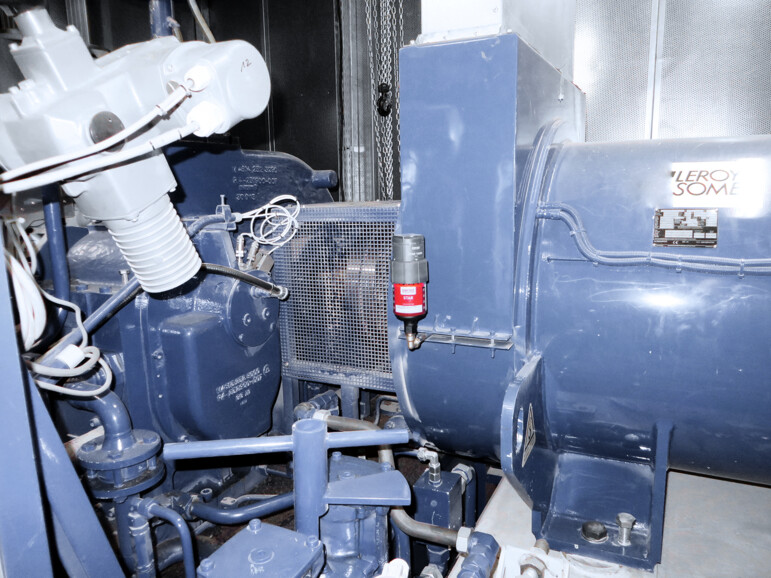
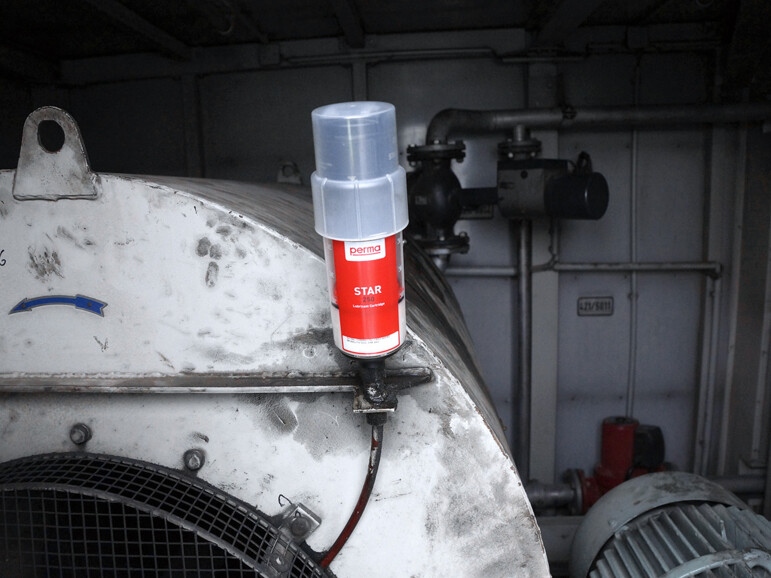
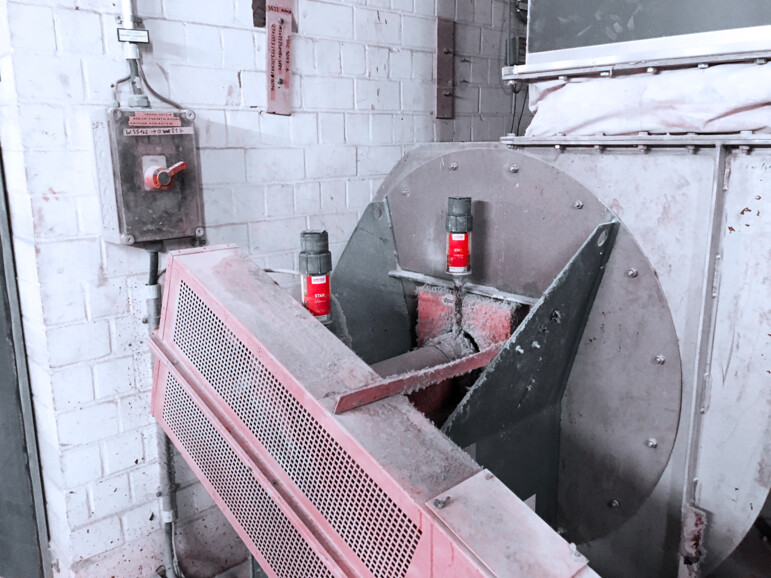
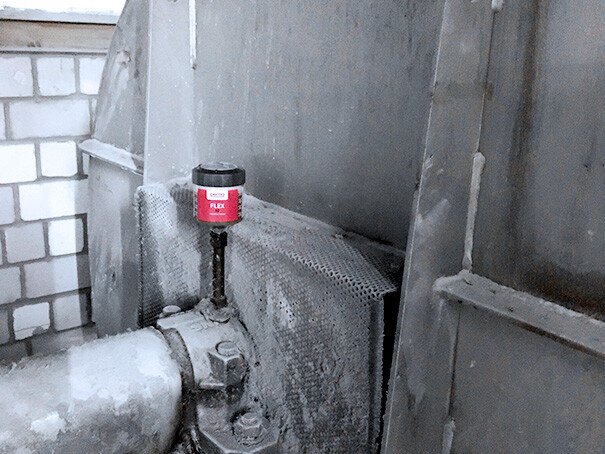